Future of STEEL Manufacturing Factories: From Raw Material Extraction to Finished Steel Products
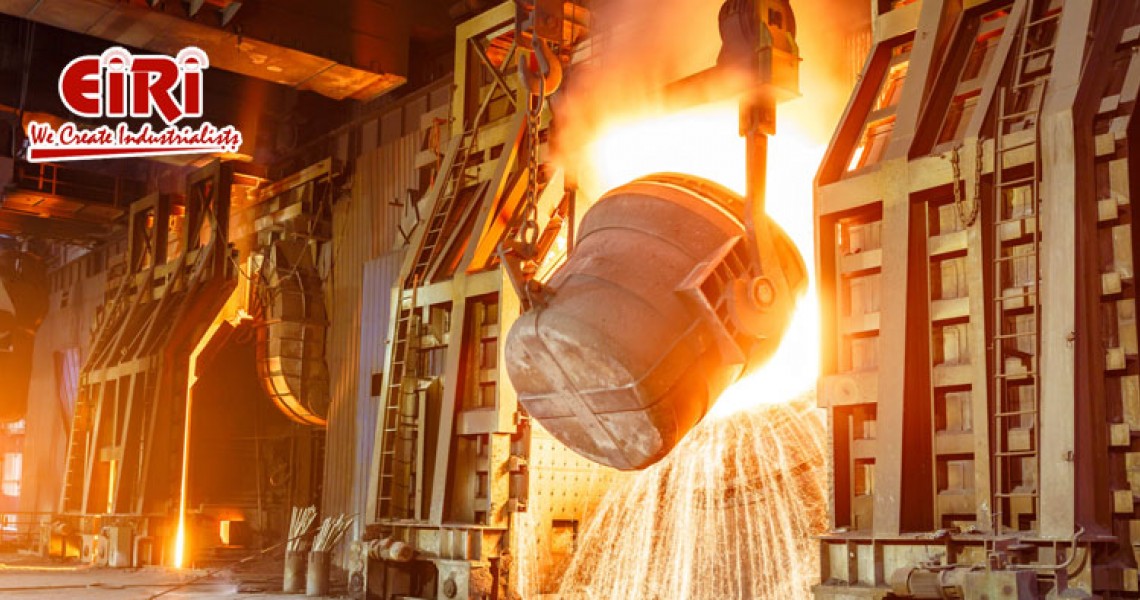
Steel is the backbone of modern civilization, shaping everything from infrastructure to appliances. As a key component in countless industries, steel manufacturing plays a pivotal role in global economic growth. This article delves into the intricacies of the steel manufacturing process, from raw material extraction to the final product, exploring technological advancements and sustainability practices that are unlocking the future of this essential industry.
The steel manufacturing process is a complex, multi-stage operation that transforms raw materials into finished steel products. It typically begins with the extraction of iron ore, a key raw material in steel production, and involves several stages to ensure the material is refined, processed, and ready for various applications.
The steel production process can be broken down into key phases:
- Raw Material Processing: Iron ore, along with other materials like coal and limestone, is mined and prepared for steelmaking.
- Ironmaking: This phase involves converting raw iron ore into liquid iron, often through smelting in a blast furnace.
- Steelmaking: The liquid iron is then further refined to reduce impurities, often in a basic oxygen furnace or an electric arc furnace.
- Casting and Rolling: After steel is made, it is cast into molds to form basic shapes, which are then rolled into final products like sheets, bars, or beams.
Steel factories operate as highly specialized industrial complexes where each stage is managed to maximize efficiency and ensure the highest quality output. A deep understanding of the steel industry reveals that the process requires precise control of temperatures, chemistry, and mechanical processes to ensure that the final steel products meet strict specifications for various industries.
The Importance of Raw Material Extraction in STEEL Manufacturing
Raw material extraction is the first critical step in steel manufacturing. The majority of steel is made from iron ore, a naturally occurring mineral. This iron-rich ore is typically mined in large quantities from the earth's crust using modern mining processes. In addition to iron ore, other raw materials for steel production include coal (which is converted into coke) and limestone, both of which play important roles in the steelmaking process.
Iron ore extraction is a global industry, with major producers in regions like Australia, Brazil, and China. The raw material supply chain is crucial to steel manufacturing, as the availability and cost of raw materials directly impact production capacity and pricing.
Sustainability is becoming increasingly important in the sourcing of these materials. Sustainable sourcing of raw materials aims to reduce the environmental footprint of mining operations, ensuring that companies adhere to eco-friendly practices while still meeting the high demand for steel. Sustainable mining techniques, such as using renewable energy sources and minimizing water usage, are integral to the future of raw material extraction in the steel industry.
Processing Raw Materials: Turning Ore into Steel Ready for Production
After extraction, the raw materials undergo several processing stages before they can be used in steel production. The first step is smelting iron ore, a process in which the ore is heated in a blast furnace with coke and limestone to remove impurities. This results in molten iron, or "pig iron," which is further refined to produce steel.
Raw material processing techniques are critical in ensuring the quality and consistency of the steel produced. Refining processes in steelmaking involve the removal of excess carbon and other impurities to create high-quality steel. Techniques such as oxygen blowing and electric arc furnace methods are used to convert iron into steel.
In modern factories, metallurgical processes ensure that the chemical composition of the steel is precisely controlled to meet the demands of various industries. Steel is then cast into ingots, blooms, or slabs, which are later rolled into sheets or shaped into beams, bars, and other final products.
The Role of Technology in Modern STEEL Factories: Innovations Driving Efficiency and Quality
The steel industry has evolved significantly over the past few decades, with advancements in technology transforming how steel is produced. One of the key innovations is the rise of automation in steel manufacturing, where robots, automated machinery, and computer-controlled systems manage much of the production process.
Advanced manufacturing technologies are helping steel factories operate with greater efficiency and precision. AI in steel production allows for real-time monitoring of machinery, predictive maintenance, and optimized production cycles. AI algorithms can detect potential issues before they lead to costly breakdowns, reducing downtime and improving overall productivity.
The concept of smart factories in the steel industry is also gaining traction. These factories use a combination of digital technologies, sensors, and cloud computing to monitor every aspect of the production process, from raw material intake to the final product. Quality control measures are significantly enhanced in such factories, where defects can be detected early in the process, ensuring higher-quality steel output.
Diverse STEEL Products: From Beams to Bars - Understanding Their Applications and Markets
The diversity of steel products is vast, with different grades and forms tailored to specific applications. From steel beams used in the construction of skyscrapers to steel bars essential for reinforced concrete, steel products play a critical role in nearly every industry.
Applications of manufactured steel products range from:
- Construction: Steel beams, columns, and trusses are essential for the structural framework of buildings, bridges, and infrastructure.
- Automotive: High-strength steel is used in vehicle manufacturing to enhance safety and durability.
- Energy: Steel is used in pipelines, wind turbines, and other energy infrastructure.
- Manufacturing: Steel forms the backbone of machinery, tools, and factory equipment.
The market demand for steel items continues to grow, driven by ongoing urbanization, industrial development, and global infrastructure projects. Both construction-grade and industrial-grade steels have seen increased demand due to their strength, durability, and adaptability. Each type of steel product is engineered for specific uses, ensuring that industries have the materials they need for efficient operations.
Sustainability Practices in STEEL Manufacturing: Balancing Production with Environmental Responsibility
Sustainability is a major concern in steel manufacturing, as the process is energy-intensive and contributes to greenhouse gas emissions. However, the industry is making strides in reducing its environmental footprint through various sustainable practices.
One of the most important sustainability initiatives is recycling scrap metal. Steel is 100% recyclable, and the use of recycled steel reduces the need for raw material extraction and decreases energy consumption. Many steel factories now incorporate large amounts of scrap metal into their production cycles, contributing to a circular economy in the metals industry.
Emissions reduction strategies are also being implemented in steel manufacturing. Factories are adopting cleaner energy sources, such as solar and wind, to power their operations. Additionally, new technologies are being developed to capture carbon emissions and reduce the overall impact of steel production on the environment.
Incorporating green technology for producing steels is not only beneficial for the planet but also economically viable. Factories that embrace these sustainable practices are positioned to thrive in a future where environmental responsibility is increasingly prioritized by governments, consumers, and investors.
Conclusion: Why Investing in a Reliable STEEL Manufacturing factory is Key to Future Growth and Innovation
The steel industry continues to be a cornerstone of modern industrialization, with innovations and sustainability practices shaping its future. Investing in a reliable steel manufacturing factory is not only a sound financial decision but also an opportunity to contribute to the future of sustainable construction, infrastructure, and manufacturing.
By focusing on advanced technologies, sustainable sourcing of raw materials, and efficient production methods, steel factories can remain competitive in a rapidly evolving market. Whether you’re in construction, automotive, or manufacturing, steel will continue to be a vital material, making investment in this sector a key driver of future growth and innovation.