Valve Manufacturing Plant
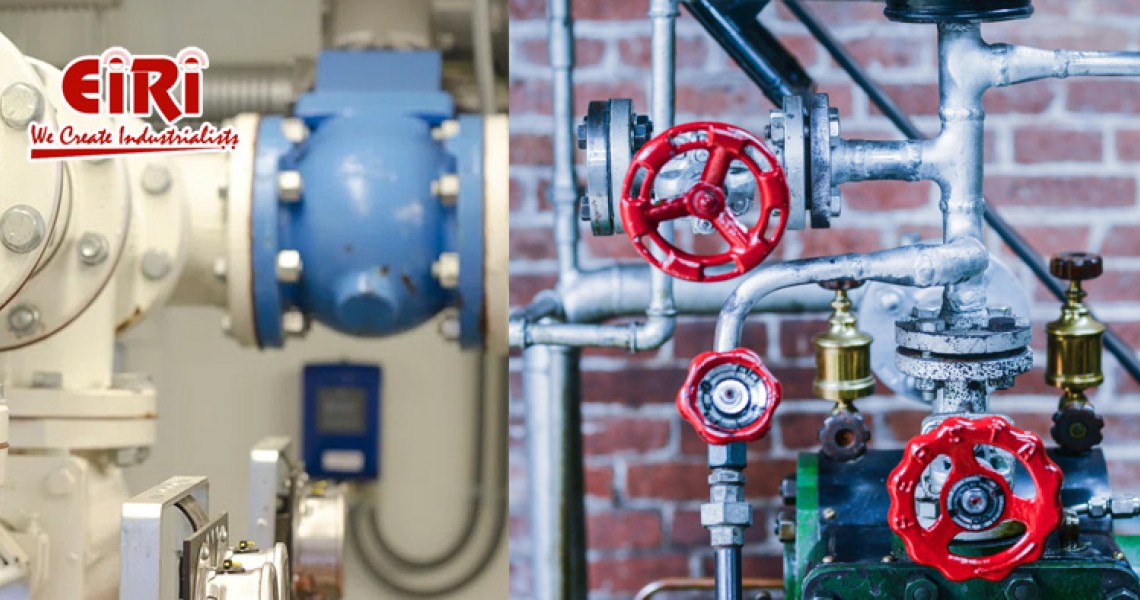
Valves are indispensable components in modern engineering and industrial systems, controlling the flow of liquids, gases, and slurries in diverse applications. These devices are vital for ensuring efficiency, safety, and control across industries such as oil and gas, water treatment, power generation, and manufacturing. A valve manufacturing plant represents a complex interplay of advanced machinery, skilled labor, and stringent quality standards. Setting up such a facility requires thorough planning, a clear understanding of market demands, and adherence to regulatory norms.
Valves come in numerous varieties, each catering to specific industrial needs. Gate valves, globe valves, ball valves, butterfly valves, check valves, and pressure relief valves are some of the most commonly used types. These valves differ in design and functionality, serving applications ranging from simple flow control to complex pressure regulation. Their design intricacies and operational precision underline the importance of a robust manufacturing process to ensure quality and reliability.
Types of Valves
- Gate Valves: Used for on/off control in pipelines.
- Globe Valves: Regulate flow and pressure in pipelines.
- Ball Valves: Offer reliable shut-off and control for a wide range of applications.
- Butterfly Valves: Compact and lightweight, ideal for high-capacity flow systems.
- Check Valves: Prevent backflow in systems.
- Pressure Relief Valves: Protect systems from overpressure conditions.
Each type of valve serves specific purposes across industries, with variations in design and material to suit different operational environments.
Key Components of a Valve Manufacturing Plant
Establishing a valve manufacturing plant begins with selecting a suitable location and infrastructure. Proximity to raw material suppliers and target markets is crucial to minimize logistics costs. The facility should include dedicated areas for casting, machining, assembly, testing, and storage. Utilities such as electricity, water supply, and waste management systems are essential for seamless operations. A well-planned layout helps streamline the production process, reducing inefficiencies and boosting productivity.
The machinery used in valve manufacturing is critical to achieving precision and durability. CNC (Computer Numerical Control) machines play a pivotal role in shaping valve components with high accuracy. Casting and forging units are employed to create valve bodies, while welding machines are used to assemble parts. Surface treatment units, such as those for electroplating or powder coating, enhance the resistance of valves to corrosion and wear. Additionally, testing equipment ensures that the finished products meet safety and operational standards.
Materials Used in Valve Manufacturing
The choice of materials is fundamental to the performance and longevity of valves. Metals such as stainless steel, brass, bronze, cast iron, and alloys are commonly used for valve bodies due to their strength and corrosion resistance. Internal components, such as seals and discs, often employ polymers like PTFE (Polytetrafluoroethylene) or rubber for their non-reactive and flexible properties. Advanced coatings, such as anti-corrosion and heat-resistant layers, further enhance the durability of valves, especially for use in harsh environments.
The Valve Manufacturing Process
The valve manufacturing process is an integration of engineering precision and quality assurance. It begins with the design phase, where engineers create detailed schematics tailored to specific applications. Prototyping follows, allowing manufacturers to test initial designs for performance and feasibility.
The production phase starts with casting or forging, where metals are shaped into valve bodies. Casting involves pouring molten metal into molds, while forging applies high pressure to shape heated metal. Once the raw bodies are prepared, they are machined using CNC technology to achieve precise dimensions. Machining is critical for creating intricate internal passages and external threads that ensure compatibility with pipelines and other systems.
Assembly is the next crucial step, where internal components like discs, seats, and seals are fitted into the valve body. Skilled workers or automated systems ensure that each part is aligned perfectly. The assembled valves then undergo rigorous testing, including pressure tests to check for leaks and functionality tests to confirm operational efficiency. Finally, surface treatments like coating or painting are applied to protect the valves from environmental damage.
Applications of Valves
Valves are versatile components used across various sectors. In the oil and gas industry, they are essential for drilling, refining, and transporting hydrocarbons, with high-pressure valves ensuring safety and efficiency. Water treatment plants rely on valves to regulate flow and maintain pressure in distribution systems. In power generation, valves control the flow of steam, gas, and water, ensuring optimal performance and safety.
Chemical and petrochemical industries require valves capable of withstanding corrosive substances and high temperatures. Food and beverage processing plants use sanitary valves designed for cleanliness and hygiene. Even in pharmaceuticals, valves are critical for maintaining sterile conditions and precise control over fluid handling systems. These diverse applications underline the universal importance of valves in industrial and everyday settings.
Valves are integral to numerous industries, each requiring specific types and designs.
1. Oil and Gas
- Used in drilling, refining, and transportation of hydrocarbons.
- High-pressure valves are essential for safety in pipelines.
2. Water Treatment
- Regulate the flow of water in purification and distribution systems.
- Prevent backflow and control pressure in municipal water supplies.
3. Power Generation
- Valves are critical in controlling steam, gas, and water flows in thermal and nuclear power plants.
4. Chemical and Petrochemical
- Handle corrosive and high-temperature fluids in production and storage systems.
5. Food and Beverage
- Sanitary valves are used in processing liquids like milk, beverages, and oils.
6. Pharmaceuticals
- Maintain sterile conditions in manufacturing and distribution of drugs.
Market Dynamics and Growth Prospects
The global valve market is expanding rapidly, driven by urbanization, industrialization, and technological advancements. The demand for valves is particularly high in emerging economies, where infrastructure development and energy needs are accelerating. In developed markets, the adoption of smart and automated systems is creating opportunities for advanced valve technologies.
Urbanization and infrastructure development are significant drivers of market growth. As cities expand, the demand for water supply systems, power plants, and industrial facilities increases, boosting the need for high-quality valves. The growing emphasis on energy efficiency and renewable energy projects also contributes to market expansion, with valves playing a key role in regulating systems in solar, wind, and hydroelectric power plants.
Challenges in Valve Manufacturing
Despite its potential, the valve manufacturing industry faces several challenges. The fluctuating costs of raw materials, such as metals and alloys, can impact profitability. Energy consumption is another concern, as the production process involves energy-intensive activities like casting, machining, and testing. Manufacturers must also navigate strict regulatory standards to ensure safety and environmental compliance, which can increase operational costs.
Counterfeit products pose a significant threat to the industry, undermining trust in established brands. These low-quality imitations often fail to meet safety standards, leading to system failures and reputational damage. Additionally, the fast pace of technological advancements requires manufacturers to invest continuously in research and development to stay competitive.
Technological Advancements in Valve Manufacturing
Innovation is at the forefront of the valve manufacturing industry. Smart valves, integrated with IoT (Internet of Things) technology, enable remote monitoring and control, improving efficiency and safety. These valves are particularly useful in industrial automation, where real-time data can optimize operations and reduce downtime.
Advanced materials, such as composite alloys and high-performance polymers, are being used to create lightweight yet durable valves. These materials enhance performance while reducing manufacturing costs. Additive manufacturing, or 3D printing, is another breakthrough, allowing for rapid prototyping and production of custom-designed valves with intricate geometries.
Sustainability in Valve Manufacturing
Sustainability is becoming a priority in the valve manufacturing industry. Companies are adopting eco-friendly practices, such as recycling scrap materials and reducing waste during production. Energy-efficient machinery and processes are being implemented to minimize the environmental impact. Some manufacturers are also exploring biodegradable materials and coatings to align with global efforts to reduce carbon footprints.
Opportunities for Entrepreneurs
The valve manufacturing industry offers significant opportunities for entrepreneurs. Emerging markets in Asia, Africa, and the Middle East present a growing demand for high-quality valves, driven by infrastructure projects and industrial development. Export potential is another lucrative avenue, with developed countries seeking cost-effective solutions from reliable suppliers.
Entrepreneurs can also explore niche markets, such as valves for renewable energy systems or specialized applications like pharmaceuticals and food processing. Providing value-added services, such as customization, installation, and maintenance, can further enhance competitiveness in this dynamic industry.
Conclusion
Valve manufacturing is a dynamic and essential industry that underpins the functioning of numerous sectors. From simple flow control to complex automation systems, valves are indispensable for ensuring safety, efficiency, and reliability. Establishing a valve manufacturing plant requires a strategic approach, encompassing advanced technology, skilled labor, and adherence to quality standards.
As the global demand for valves continues to grow, driven by infrastructure development, energy needs, and technological advancements, the industry presents immense opportunities for growth and innovation. By embracing sustainability and staying ahead of market trends, valve manufacturers can position themselves as leaders in this vital sector.