Modern Technology Of Injection Moulding, Blow Moulding, Plastic Extrusion, Plastic Pipes, Pet Bottle & Others Plastics Industries
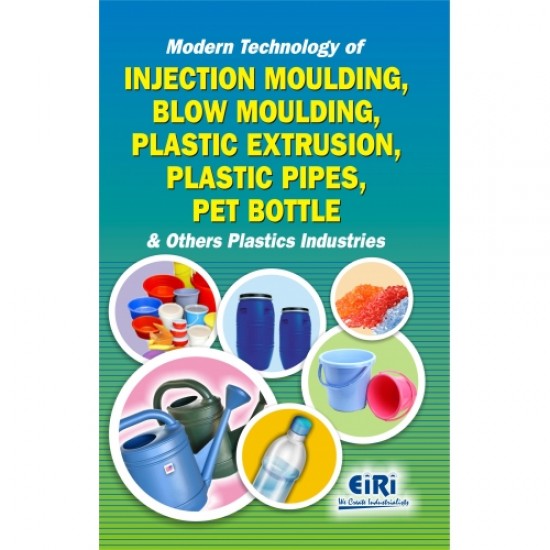
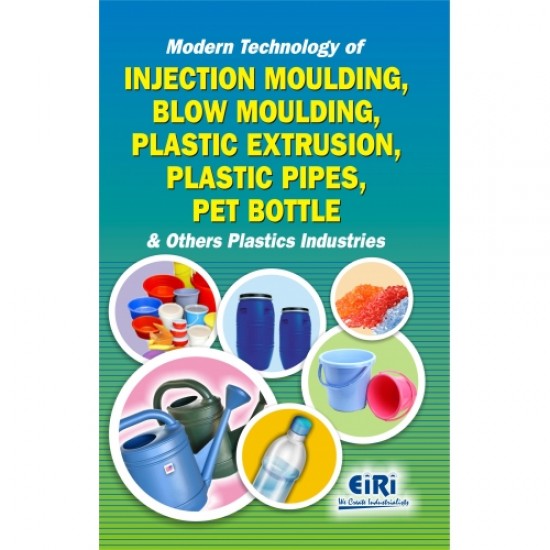


- More than 40 years of experience
- Managed by expert industrial consultants
- ISO 9001-2015 Certified
- Registered under MSME, UAM No: DL01E0012000
- 24/5 Research Support
Get your quesries resolved from an industry expert. Ask your queries before report or book purchase. - Custom Research Service
Speak to the our consultant to design an exclusive study to serve your research needs. - Quality Assurance
All reports are prepared by highly qualified consultants & verified by a panel of experts. - Information Security
Your personal & confidential information is safe & secure.
The book Modern Technology of Injection Moulding, Blow Moulding, Plastic Extrusion, Plastic pipes, pet Bottle & others plastics industries covers Blow Moulding, Characteristics of HDPE and PP Polymers for Blow Moulding, Moulds for Blow Moulding, Plastic Extrusion, Fuels from Plastics Waste, FRP Silos, Tanks and Pipes by Centrifugal Casting , Injection Moulding fluid Assisted Injection Moulding Makes Hollow Parts Faster, Lighter, Italian Equipment for Plastics Recovery, Injection Moulding of Plastics, Mould and Machine Setting up, Operations and Controls in Injection Moulding, Industrial Method for the Manufacture of Low Density Polyethylene, Injection Moulded Goods, Jelly Filled Cables, Linear Low Density Polyethylene Drip Irrigation Pipes, Light Weighting Option PET Bottles, Blow Moulded Plastic Containers, HDPE, PVC & CPVC Pipes and Fittings, Pet Bottles used for Packaged Drinking Water, Edible Oils, Alcoholic Beverages (Country Liquor & IMFL) etc. (in Cap: 500 ml, 1 ltr, 2 ltrs, 5 ltrs), Plastic Injection Moulded Items (Like Buckets, Plastic Chairs, Bathing Tub), Plastic Injection Moulding, Blow Moulded and PET Bottles Products, Plastic Waste Recycling Unit.
BLOW MOULDING
- Injection blow Moulding
- Extrusion Blow Moulding
- Intermittent Extrusion
- Stretch Blow Moulding
- Properties of the most common plastics bottle materials
- Injection Moulded Parison
- Extruded Parison
- Extrusion Blow moulded Parison
- Aseptic Blow Moulding
- Multilayer Blow Moulding
- Injection versus extrusion blow moulding
- Blow Moulding Process
- A typical extrusion blow moulding machinery
- Quick mould change system blow moulding
- Blow Mould
- Injection blown vis a vis extrusion blow
- Moulding
- Injection blow moulding
- Quick Change Plate
- Blow Pin (s)
- Article transfer
- Punch
- Die/Pin
- Head
- Characteristics of extrusion blow moulding of some common polymers
- Major uses of composite bottles
- Coextrusion which Plastics go best together
- Extrusion blow moulding Design Concepts
- Blow moulding
- Perforator for drainage pipes
- Reciprocating screw machine used in blow moulding
- Die and mandrel assembly
CHARACTERISTICS OF HDPE AND PP POLYMERS FOR BLOW MOULDING
- HDPE High Density Polyethylene
- Polypropylene
- Selection of Blow Moulding Material
- Recommended temperature for cavities in blow moulds
- Melt temperature and pressure for extrusion blow moulding of some polymers
- Processing data for stretch blow moulding
- Volume shrinkage of stretch blow moulded bottles
- Average polymer swell for some polymers
- Data on air blowing pressures
- Operation and Control in Blow Moulding
- Bottle Design Concepts
- Basic design consideration in blow moulding
- Bottle design concepts
- Surface treatment of containers
- Flame Treatment
- Coatings
- Fluorination
- Sulphonation
- Bar coading
- Package Coding
- Blow ratio
- Shape of cavity opening
- Some blow moulding process variants
- Deep draw blow moulding
- Flashless Blow Moulding (FBM)
- Extrusion blow mould check list
- Multilayer Blow Moulding
- Industrial Blow Moulding Applications
- Co-extrusion Blow Moulding
- Advantages of Co-Extrusion of Large Parts
- Multilayer Blow Moulding
- Six Factors that can change container volume
- Comparison
- Intermittent Vs Continuous Co-extrusion
- Why Multilayer containers
- Multilayer film Major Applications
- Commercial co-extrusion
- Co-ex/multilayer injection moulding
- Multi component moulding
- Multicolour Moulding
- Special Moulding
- Multilayer plastics bottles
- Main Function
- Materials
- Observation
- Blow moulding some new technologies
- 3-Dimensional Blow Moulding
- Coextrusion properties of materials
- Applications/structures of multilayer bottles
- Preferred Materials Combination
- Rotary injection blow moulding
- 15% Long Glass Fiber
- Foam Technology
- Rotary Injection blow moulding
- Extrusion blow mould check list
MOULDS FOR BLOW MOULDING
- Bottle Design Concepts
- Some General Design considerations
- Bottle pack process
- Industrial and Structural part Design
- Extrusion Blow Moulds
- Construction
- Blow moulds
- The Materials
- Cooling
- Pinch-offs
- Venting
- Injection Blow Moulding
- Injection Blow Moulding Process
- Injection blow moulding
- Strtech blow moulding
- Single stage per process
- Injection stretch blow moulding
- Coextrusion Blow Moulding
- Pet stretch Injection blow moulding
- Injection Stretch Blow Moulding Process
- Types of Processes
- Development of PP Containers
- ISBM Machines for PP
- Opportunities for PP Containers
- Bottles and Containers Market
- Compact preform shuttle system
- Conclusion
- Shuttle mould for increasing output of pet preforms
PLASTIC EXTRUSION
- Single screw extruder
- Extruder barrel and feed section
- Barrel heat input and extraction mechanisms
- Barrel temperature control system
- Screw
- Gearbox and thrust bearing
- Drives
- Venting
- Types of Dies for Film Extrusion
- Extrusion of plastic films
- Introduction
- Processing
- Material of construction
- Heating & Cooling systems
- Breaker Plate & Screeens
- Downstream Equipments
- Different types of Film Processing techniques
- Blown Film Extruder
- Processing temperature profiles
- Frost Line height (FLH)
- Film Thickness Control
- Thickness Variation Control
- Stretch Extrusion Process
FUELS FROM PLASTICS WASTE
- Introduction
- Global Scenario
- Plastic Waste
- Environmental Impact
- Plastic waste importers in Asia
- Fuel/Energy Shortage
- Alternative Waste Disposal Methods
- Plastic waste to fuel
- Conversion Process
- Principles Involved
- Calorie on a par with Coal and Oil
- Laboratory Scale
- The Process
- Salient Features
- Test Reports
- Emission Report
- End Uses
- Liquid Hydrocarbon
- Gas
- Solid Hydrocarbon
- Gas
- Solidfuel
- Benefits of the Technology
FRP SILOS, TANKS AND PIPES BY CENTRIFUGAL CASTING
- Introduction
- Product Description and properties
- Uses and Applications
- Silos for storage and processing
- Performance Characteristics of Silos Made of Different Materials
- Tanks for storage and transport
- Pipes
- Cylindrical bodies as constructional elements
- Manufacturing Process
- Raw Materials
- Plant and Machinery
INJECTION MOULDING FLUID ASSISTED INJECTION MOULDING MAKES HOLLOW PARTS FASTER, LIGHTER
- Gas assisted injection moulding
- How does it work
- The process sequence
- Geometric catgories
- Merits of gas assist injectio moulding process
- Geometric categories of gas assisted injection molded products
- Complex Parts with Localized heavy Sections
- Rod shaped Parts
- Large Cover Shaped Parts
- Demerits of gas assisted injected molding
- Gas assisted injection molded products
- Application examples
- Water assist injection molding
- Melt/Gasfront velocity amount of polymer in front of the gasbubble
- Gas bubble propagation wall thickness distribution
- Short shot process
- Push back process
- Overflow process
- Flow Process
- Advantages of the WIT
- Conclusion
ITALIAN EQUIPMENT FOR PLASTICS RECOVERY
- Shredding and grinding of car bumpers
- Two and three shafts
- Profiles and offcuts
INJECTION MOULDING OF PLASTICS
- The Material Hopper
- The Barrel/Cylinder heating system
- The Barrel/Cylinder and Screw
- Adhesion
- Abrasion
- Corrosion
- Delamination
- The Screw Drive System
- The Stationary Platen
- The Mould
- The Moving Platen and Tie Rods
- The Clamping Unit
- To close and open the mould
- To eject the parts
- To keep the mould closed during the injection cycle
- Trouble free moulds
- General check list for new moulds
- Machine
- Mould Design
- General
- Mould Analysis Software
- Co-ordinate Measuring Machine
- Benefit to Processors
- Granulator Check List
- Metal Separators
- General Performance Data
MOULD AND MACHINE SETTING UP
- Moulding Set up Time
- Injection moulding cycle
- A break up of most common moulding cycle
- Check list for start up
- Processing :Some initial consideration
- Preliminary
- Machine Requirement
- Number of shots/Cycle
- Time
- Plasticizing Capacity/Rate
- Clamp Tonnage
- Mouldability features
- part Removal
- The Sprue
- runner System
- Cold Slug Well
- Gate Location
- Gate Size
- Cores
- Vents
- Undercuts
- Melt Rheology
- Purging
- The Injection Moulding Machine Operation
- The injection moulding cycle
- Sequence of events during an injection moulding cycle
- Injection moulding cycle
- Trace of two different injection moulding cycles in a pvt diagram
- Holding pressure
- Schematic of different runner system arrangements
- Principal conditions in moulding
- Schematic of different gating system
- SMC production line
- Setting up a moulding shop
- Accessories for the Injection Unit
- Measurable minimum requirement for injection moulding machines
- Hygroscopic Plastics
- Frequently Employed Clamping Systems for Injection Moulding Machine
- Injection pressure required for various plastics
- Common Gating Systems & Their Aplications
- Recommendation for temperature settings along a vented barrel for various thermoplastics
- Spherical radi and of dimensions of nozzles according to european standards
OPERATIONS AND CONTROLS IN INJECTION MOULDING
- Effect of processing on mechanical properties
- Injection moulding parameters for common plastics
- Molecular Orientation
- Residual Stresses
- Melt Elasticity
- Melt Fracture
- Weld Lines
- Accurate Dimensions
- Cooling Rate
- Weigh Feeding and Blending
- Feeders
- Shrinkage in direction of flow (a) and Transversely to it (b) with various types of gate
- Weight Blenders
- Interrelationship of part design, moulding conditions, polymer selection and mould design
- Specific gravity and bulk factor of plastics materials
- Controls
- Thermal conductivity of materials
- Water absorption of common plastics(%)
- Process control Methods in injection moulding
- Factors that Affect Reproductive behaviour of Injection moulding Machine
- Minimum actual cooling time in seconds
- Processing temperatures, mould temperatures, and shrinkage of most common plastics used in injection moulding
- General
- In line injection compression equipment
- Mouldflow
- What is Mouldflow
- Measurable minimum requirements for injection moulding machines
- Dry cycle times of injection Moulding machines a thumb rule
- How Mouldflow can help Part Designers, Mould Maker & Processor
- How Mouldflow can help Mould Designer
- How Mouldflow can help a Processor
- How to improve Quality & Productivity using Mouldflow
- Injection pressure required for various plastics in general
- Injection pressure ranges for modular system of injection units
- Effect of processing parameters on part dimensions
- Processing Limitations for various polymers guidelines
- Recommended nozzles for plastics moulding machines
- Percentage by weight of permissible moisture and the recommended drying temperatures of various plastics materials
- Conventional injection moulding machine
- Remplan's line injection compression system
- Injection moulding processing temperature range
- Interrelationship of part with design, moulding conditions, polymer selection and mould design
- Suggested wall thickness for common thermoplastic moulding materials
- Hydraulic system noise suppression
- Some suggestions for Noise Reduction
- Composition of material(%) after being processed several times (number of throughputs and with different ratios of virgin-regrind)
- Comparison of colouring methods
- Wall thickness of moulded parts
- Quality of moulded parts factory that affect
- Injection moulding section
- Estimating Cooling Time
- Importance of cooling in injection moulding
- Good Cooling vs. Bad Cooling
- Why is Turbulent Flow important
- How Cooling Affects the Cycle Time
- How Wall Thickness Impacks Cooling Time
- Cooling channel
- Diameter and Placement
- How Turbulent is Enough
- Energy Consumption in Injection Moulding
- Typical break up of energy in injection moulding cycle
- Injection moulding control system
- Mechanical Properties
- Dimensional Accuracy
- Surface Quality
- Basic Methods for control
- Temperature Controls
- Injection moulding product to production
- Starting a new unit/new job
- Pressure Measurement
- Disturbing Factor that affect smooth operation
- Clamping
- Injection
- Microprocess controls in moulding
- Standard Functions
- Monitoring Functions
- Control Functions
- Injection moulding pressure conversion table
- Injection moulding clamp force conversion table
- Injection moulding shot weight conversion factors
- Injection moulding shot volume conversion table
INDUSTRIAL METHOD FOR THE MANUFACTURE OF LOW DENSITY POLYETHYLENE
- Flow chart for the manufacture of LDPE
- Mechanism
- Properties
- Physical Properties
- Chemical Properties
- Propagation
- Termination
- Uses
INJECTION MOULDED GOODS
- Introduction
- Product Description and Properties
- ABS
- Filled Polypropylene
- Properties & Applicatin of Filled Polypropylene
- Polypropylene Copolymer
- Uses and Applications
- Manufacturing Process
JELLY FILLED CABLES
- Introduction
- Product Description and Properties
- Uses and Applications
- Manufacturing Process
LINEAR LOW DENSITY POLYETHYLENE DRIP IRRIGATION PIPES
- Need for Plasticulture
- Plasticulture
- Indian Trend-Drip Irrigation
- Recurrent drought and scarce water resource has led to inefficient water use
- Drip Irrigation
- Advantages of Drip Irrigation Systems
- Drip irrigation system includes the Main Line, Submain, Line, Laterals & Emitters/Drippers
- Micro Irrigation
- Benefits
- Status in India
- Objectives of Micro Irrigation System
- Comparison between Conventional Irrigation v/c Micro Irrigation
- Manufacturing Process
- Advantages of using LLDPE
- Business with Plasticulture
- Polyethylene Pipes for Entrepreneurs
- Conslusion
LIGHT WEIGHTING OPTION PET BOTTLES
- Why light weighting of PET bottles
- Savings delivered by light weighting PET bottles
- Options for light weighting of PET bottles
- Weight reduction from neck area
- Closure manufacturer
- CSD thread evolution
- Conversion from PCO 1810 to PCO 1881 neck gives total savings of 1.9 gm per bottle
- Why this change has not happened in Indan maket?
- What is the next cost effective option
- Mineral water thread evolution
- Estimated savings with modified pco 1810
- light weight neck (3,9 gm)
- What is the optimum neck weight for mineral water application
- Comparison of two necks
- Light weighting of pre form by reduction of body weight
- Light weighting of pre form by reduction of bottom part weight
- Light weighting of PET bottle by reduction in closure weight
BLOW MOULDED PLASTIC CONTAINERS
- Introduction
- Process of Manufacture
- Extrusion Blow Moulding
- Storage of Bottles
- Storage of empty containers
- Transport of Containers
- Plant Economics of Blow Moulded Plastic Containers
- Plant & Machinery
- Process Flow Diagram for Polyethene Bottles
- Fixed Capital
- Raw Materials
- Total Working Capital/Month
- Total Capital Investment
- Turn Over/Annum
HDPE, PVC & CPVC PIPES AND FITTINGS
- Chemical Resistance
- Strength
- Internal Corrosion Resistance
- External Corrosion Resistance
- Freedom from Toxicity Odors, Tasters
- Corrosion Free
- Low Friction Loss
- Low Thermal Conductivity
- Easy installation and low installation cost
- Maintenance free Standard Approved
- Plant Economics of HDPE, PVC & CPVC Pipes and Fittings
- Plant & Machinery
- Process Flow Sheet for The Manufacture of PVC Pipes
- Process Flow Diagram for CPVC Pipes
- Fixed Capital
- Raw Materials
- Total Working Capital/Month
- Total Capital Investment
- Turn Over/Annum
PET BOTTLES USED FOR PACKAGED DRINKING WATER, EDIBLE OILS, ALCOHOLIC BEVERAGES (COUNTRY LIQUOR & IMFL) ETC. (IN CAP: 500ML, 1 LTR, 2 LTRS, 5 LTRS)
- Manufacturing Process of Pet Bottles ( By Single Stage Process)
- Plant Economics of Pet Bottles in Cap: 500ML
- Plant and Machinery
- PET Preform (Assorted Sizes)
- PET Bottles to Market
- Fixed Capital
- Raw Materials
- Total Working Capital/Month
- Total Capital Investment
- Turn Over/Annum
PLASTIC INJECTION MOULDED ITEMS (LIKE BUCKETS, PLASTIC CHAIRS, BATHING TUB)
- Manufacturing Process
- Plasticizing
- Injection
- After-Filling
- Time Cycle
- Process Flow Sheet
- Plant Economics of Injection Moulded Plastic Components
- Plant and Machinery
- Fixed Capital
- Raw Materials
- Total Working Capital/Month
- Total Capital Investment
- Turn Over/Annum
PLASTIC INJECTION MOULDING, BLOW MOULDED AND PET BOTTLES PRODUCTS
- Manufacturing Process
- Injection Moulding Process
- Plasticizing
- Injection
- After Filling
- Cooling and Mold Release
- Time Cycle
- Injection Moulding
- Blow Moulding Process
- Process of Manufacture
- Extrusion Blow moulding
- Storage of Containers
- Storage of empty containers
- Transport of Containers
- Pet Bottles Manufacturing Process
- Plant Economics of Plastic and Pet Bottles with caps
- Plant & Machinery
- Fixed Capital
- Raw Materials
- Total Working Capital/Month
- Total Capital Investment
- Turn Over/Annum
PLASTIC WASTE RECYCLING UNIT
- Plant Economics
- Plastic Granules from Waste
- Basis
- Manufacturing process flow sheet for Plasti Granules from Plastic Scrap
- Land & Building
- Plant & Machienry
- Other Fixed Assets
- Fixed Capital
- Working Capital Requirement/Month
- Raw Materials
- Salary & Wages/Month
- Utilities and Overheads
- Total Working Capital/Month
- Cost of Project
- Total Capital Investment
- Cost of Production/Annum
- Turn Over/Annum
- Break Even Point (.B.E.P.)
- Resources for Finance
Engineers India Research Institute (EIRI) is a renowned name in the industrial world for offering technical and financial consultancy services.
EIRI services are:
- Detailed Feasibility Reports
- New Project Identification
- Project Feasibility and Market Study
- Identification of Lucrative Industrial Project Opportunities
- Preparation of Project Profiles / Pre-Investment and Detailed Feasibility Studies,
- Market Surveys / Studies, Market Survey Cum Detailed Techno-Economic Feasibility Reports
- Project Reports in CD Roms
- Identification of Plant /Process/Machinery and Equipment, Industrial General Guidance for setting up new industrial projects.
Our most up-to-date and Technologically Advanced Industrial Project Reports, categorized with respect to Financial Outlays and Sector – wise Classification are immensely useful for :
Existing Small or Medium Scale Industrialists facing competition from large houses
Young Entrepreneurs dreaming to start their own industrial enterprise
Young Graduates and Professionals wishing to begin their career
Industrialists interested in Debottlenecking their capacities & New Product – Lines
Large Industrial Houses pursuing Expansion, Growth and Diversification Plans
How to Make Project Report?
Detailed Project Report (DPR) includes Present Market Position and Expected Future Demand, Technology, Manufacturing Process, Investment Opportunity, Plant Economics and Project Financials. comprehensive analysis from industry covering detailed reporting and evaluates the position of the industry by providing insights to the SWOT analysis of the industry.
Each report include Plant Capacity, requirement of Land & Building, Plant & Machinery, Flow Sheet Diagram, Raw Materials detail with suppliers list, Total Capital Investment along with detailed calculation on Rate of Return, Break-Even Analysis and Profitability Analysis. The report also provides a birds eye view of the global industry with details on projected market size and then progresses to evaluate the industry in detail.
We can prepare detailed project report on any industry as per your requirement.
We can also modify the project capacity and project cost as per your requirement. If you are planning to start a business, contact us today.
Detailed Project Report (DPR) gives you access to decisive data such as:
- Market growth drivers
- Factors limiting market growth
- Current market trends
- Market structure
- Key highlights
Overview of key market forces propelling and restraining market growth:
- Up-to-date analyses of market trends and technological improvements
- Pin-point analyses of market competition dynamics to offer you a competitive edge major competitors
- An array of graphics, BEP analysis of major industry segments
- Detailed analyses of industry trends
- A well-defined technological growth with an impact-analysis
- A clear understanding of the competitive landscape and key product segments
Need Customized Project Report?
- Ask for FREE project related details with our consultant/industry expert.
- Share your specific research requirements for customized project report.
- Request for due diligence and consumer centric studies.
- Still haven't found what you're looking for? Speak to our Custom Research Team
About Engineers India Research Institute:
Note: We can also prepare project report on any subject based on your requirement and country. If you need, we can modify the project capacity and project cost based on your requirement.
Our Clients
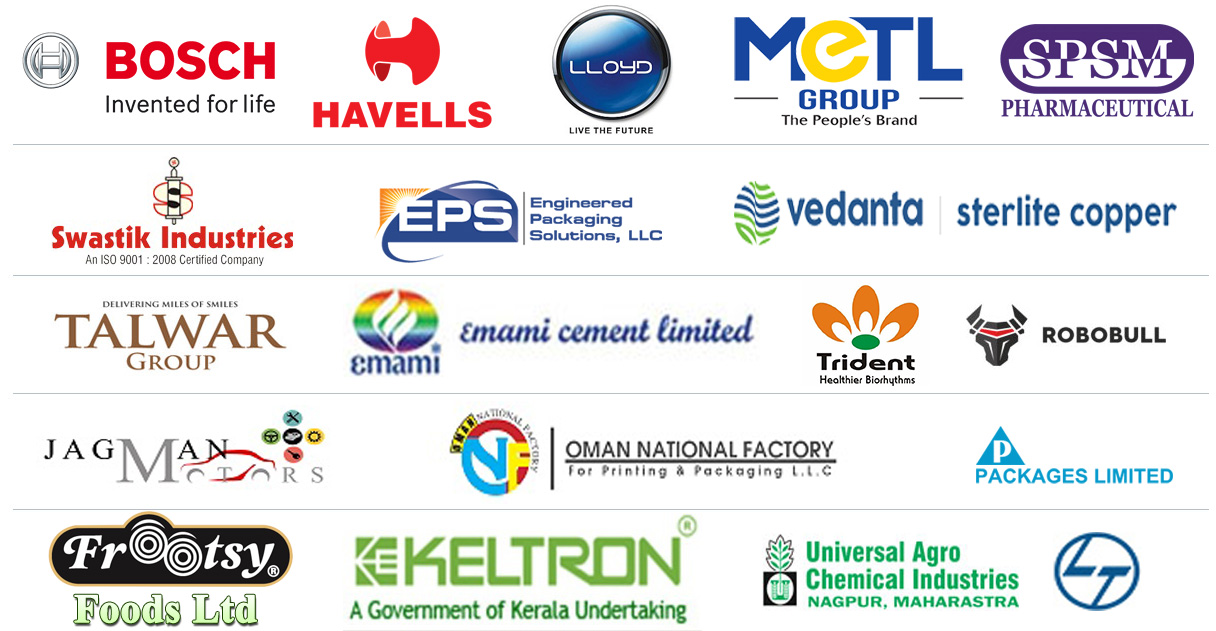
Our Approach
- Our research reports comprehensively cover Indian markets (can be modified as per your country), present investigation, standpoint and gauge for a time of five years*.
- The market conjectures are produced on the premise of optional research and are cross-accepted through associations with the business players
- We use dependable wellsprings of data and databases. What's more, data from such sources is handled by us and incorporated into the report
Why buy EIRI reports?
- Our project reports include detailed analysis that help to get industry Present Market Position and Expected Future Demand.
- Offer real analysis driving variables for the business and most recent business sector patterns in the business
- This report comprehends the present status of the business by clarifying a complete SWOT examination and investigation of the interest supply circumstance
- Report gives investigation and top to bottom money related correlation of real players/competitors
- The report gives gauges of key parameters which foresees the business execution